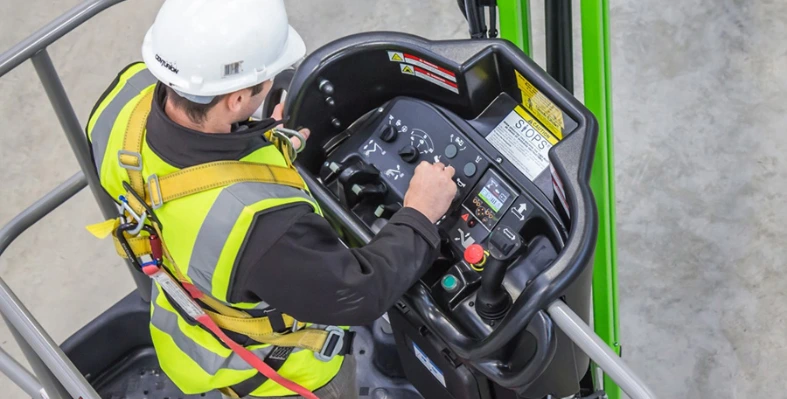
Operator safety also depends on proper use of personal fall protection equipment. (Image source: Niftylift)
Niftylift has said that it continues to advance safety in powered access equipment by focusing on the practical risks of working at height.
Although industry statistics show improvement in workplace incident rates, the company remains committed to driving further innovation through smarter engineering and user-friendly technology.
One of its standout developments is the ToughCage platform, which combines a reinforced steel cage with a robust, impact-resistant composite base.
This dual-layer protection not only shields the operator in the event of a collision but also absorbs impact energy to minimise damage to the machine’s boom and surrounding structures.
To tackle the challenges of working on sloped ground, Niftylift has equipped its MEWPs with Inclination Sensing technology.
While machines can travel across gradients beyond operational limits when booms are stowed, any attempt to elevate the booms on a slope triggers alarms and disables the drive function.
The booms must be lowered and the machine repositioned before operations can resume, preventing unsafe working conditions on unstable terrain.
If the basket is raised and the tilt angle becomes too steep, the machine automatically halts drive functions until safely reset.
Operator safety also depends on proper use of personal fall protection equipment.
Built-in safeguards
Niftylift addresses this with its intuitive ClipOn system, which provides red and green LED indicators and an audible alert to confirm harnesses are correctly attached before work begins.
Trapping incidents remain one of the most severe risks when working at height, especially if an operator is forced against the control panel.
In response, Niftylift introduced SiOPS (Sustained Involuntary Operation Prevention System) across all self-propelled machines.
SiOPS detects pressure on the control console, immediately halting all machine movements without waiting for a user response, allowing the operator to recover by simply pressing a flashing green reset button.
Further reinforcing safety protocols is Load Sensing technology, which monitors platform weight in real time.
If the system detects an overload, it disables all work functions until the weight is reduced. During operation, a recovery override allows the basket to be safely lowered first.
Supporting these built-in safeguards is Niftylink, a telematics solution that provides performance insights, real-time diagnostics, and access control.
Using PIN codes or RFID-enabled PAL cards, Niftylink ensures that only trained and authorised personnel can operate the machines, reinforcing on-site compliance and reducing the risk of human error.
Recognising that many incidents result from knowledge gaps, Niftylift also launched the NiftyPRO mobile app, an on-demand training and support tool for operators, fleet managers, and technicians.
With over 100 video tutorials covering machine operation, troubleshooting, and recovery procedures, the app bridges the gap between theoretical training and real-world application, making best practices easily accessible on-site and in the moment.
By combining smart safety features, operator-focused design, and accessible digital training, Niftylift offers a comprehensive approach to making work at height safer, more efficient, and better supported.
“Niftylift is synonymous with innovations in operator safety, introducing technologies over the years that have redefined safety standards, addressing critical risks in working at height, including entrapment, overloading, harness misuse, and unsafe tilting,” said Tom Hadden, technical sales manager, Niftylift. ‘Together, they enhance operational efficiency and provide operators with the confidence they need to work safely at height. We are committed to continuing to lead the industry in promoting safer working practices worldwide.”
Also read: Niftylift's real-time harness safety compliance in access platforms