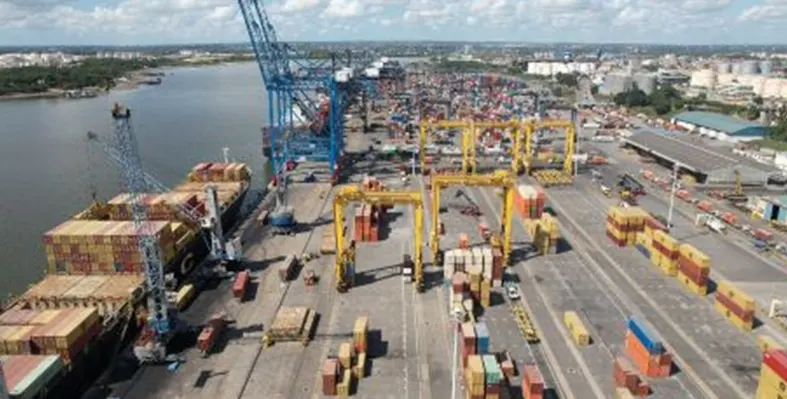
PepsiCo and DP World launch US$20mn plant in Lagos, boosting jobs, food security, and investor confidence. (Image source: DP World)
The Federal Government has reaffirmed its commitment to economic reforms and private sector-driven growth following the commissioning of a US$20 million PepsiCo and DP World production facility in Lagos
The project highlights renewed investor confidence in Nigeria’s economy and marks a significant step forward in industrial development.
The launch event was attended by senior government officials and business leaders. Speaking at the commissioning, the minister of finance and coordinating minister of the economy, Wale Edun, described the facility as evidence of Nigeria’s rising competitiveness under president Bola Ahmed Tinubu’s reform agenda.
“This is not just about two companies. It is about what is possible when global business and Nigerian ambition come together,” said Edun. “Our reforms have restored stability, unlocked investment, and are creating the conditions for rapid, inclusive growth.”
From the private sector, PepsiCo MENAPAK President Ahmed El-Sheikh emphasised Nigeria’s central role in the company’s regional strategy. He noted that the new plant demonstrates both confidence in the country’s long-term future and a commitment to sustainable investment.
Mohammed Akoojee, CEO of DP World Sub-Saharan Africa, added, “Nigeria is a key hub for Africa’s growth. Through this partnership, we are helping to build efficient, resilient supply chains that support long-term development.”
The newly inaugurated plant will produce PepsiCo’s iconic Cheetos brand, with more than 90 percent of inputs locally sourced. It is expected to generate new employment opportunities, contribute to food security, and strengthen Nigeria’s position as a manufacturing and export hub within West Africa and under the African Continental Free Trade Area (AfCFTA).
According to a statement issued by the Director of Information and Public Relations, Mohammed Manga, the investment represents a major boost for Nigeria’s economic growth. It also reinforces global investor confidence, opening fresh opportunities for businesses and citizens across the country.