In The Spotlight
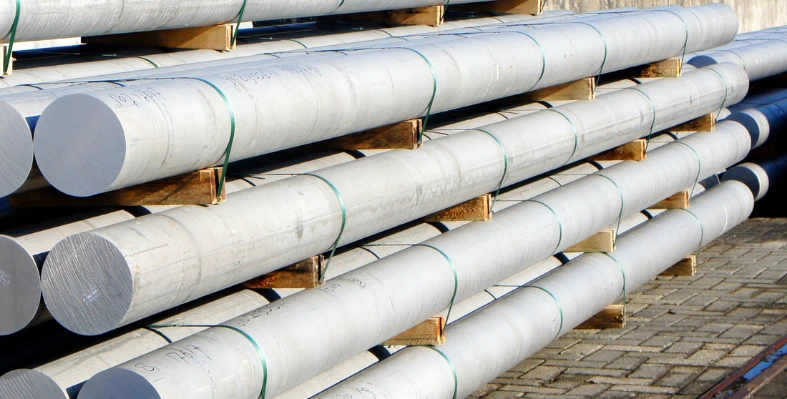
EGA is certified to the Performance Standards of the Aluminium Stewardship Initiative. (Image source: Canva Pro)
EGA can now produce ASI-certified metal
Emirates Global Aluminium (EGA) has received the Aluminium Stewardship Initiative’s (ASI) Chain of Custody Standard for its facilities in the UAE.
From the mine to the customer, this certification establishes standards for the monitoring and accounting of metal and raw materials that are produced sustainably. It is a supplement to the Performance Standard of the Aluminium Stewardship Initiative, which certifies facilities based on their sustainability performance.
Some of the raw materials used in EGA's plants in the UAE come from upstream suppliers that have earned ASI Performance Standard and Chain of Custody certification. As a result, EGA can now produce a certain amount of ASI Chain of Custody certified aluminium, giving consumers access to this type of aluminium.
Except for the recently purchased Spectro Alloys, every mining, refining, and smelting facility site owned by EGA is certified to the Performance Standards of the Aluminium Stewardship Initiative.
Global non-profit group called the Aluminium Stewardship Initiative consults with the public, civil society, end users including BMW Group and Nespresso, and aluminium producers to identify what constitutes strong sustainability performance in the aluminium industry. The international standard for sustainability in the aluminium sector is set by the Aluminium Stewardship Initiative.
DNV Business Assurance Services UK Ltd. conducted the independent, third-party audit of EGA's processes that was necessary for ASI Chain of Custody Certification.
Abdulnasser Bin Kalban, CEO of EGA, said, "Aluminium is essential for the development of a more sustainable society. It also matters how sustainably aluminium is made, and this includes sourcing of responsibly-produced raw materials. Achieving certification to the Aluminium Stewardship Initiative’s Chain of Custody Standard is step forward in our aspiration to become a global sustainability leader for the aluminium industry. I am proud the EGA is now able to produce ASI-certified metal.”
Lootah Biofuels launches smart app to boost recycling
Lootah Biofuels has launched a smart app for Android and iOS to encourage individuals and businesses across the UAE to recycle used cooking oil (UCO) into biofuel, reducing environmental and public health risks.
The app provides home collection services, an interactive map of biodiesel stations, and financial incentives through a built-in digital wallet.
Since its founding in 2010, Lootah Biofuels has built a supplier network that includes the hospitality and restaurant sectors, with the top 10 partners contributing over 300,000 litres of UCO per month.
The initiative aligns with the UAE’s sustainability goals, aiming to increase UCO recycling rates from below 50% to over 80%.
Reducing costs
The company emphasises that biodiesel from used cooking oil offers the highest carbon reduction among biofuels and can lower long-term transportation costs. The app also raises awareness about biofuels' role in reducing emissions and supports job creation in oil collection, recycling, and biodiesel distribution.
Yousif Bin Saeed Lootah, founder and CEO of Lootah Biofuels, stated, "We are committed to employing the latest technologies and solutions across all stages of our operations to accelerate the adoption of innovative and sustainable practices. Our initiatives encourage individuals and institutions to contribute to sustainability and the circular economy by leveraging available channels to collect used cooking oil and convert it into environmentally friendly and sustainable biofuel."
Biodiesel produced by Lootah Biofuels from used cooking oil has the highest carbon reduction rate among all available feedstocks for biodiesel production, according to the company.
The app, available on both Android and iOS platforms, aims to encourage individuals, businesses, and institutions across the UAE to responsibly dispose of used cooking oil. The move will divert disposal of UCO to the ground and sewerage, which poses environmental and public health risks, converting it into clean energy.
Biofuel extracted from used oil is a more cost-effective alternative, and its increasing use in commercial transportation fleet is expected to help lower the cost of goods and products in the long run.
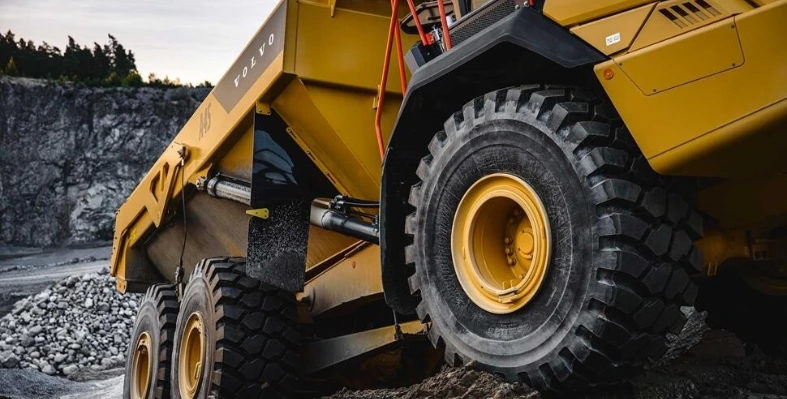
Steel is a major contributor to the carbon footprint of construction equipment. (Image source: Volvo CE)
Volvo CE's latest haulers now made with low-carbon steel
Volvo CE has begun integrating low-carbon emission steel into the serial production of all articulated haulers manufactured at its Braås facility in Sweden.
The company said that this move aligns with the company’s commitment to reducing carbon emissions across its value chain, both in machine operation and material sourcing, as part of its goal to reach net zero greenhouse gas emissions by 2040.
Steel is a major contributor to the carbon footprint of construction equipment, accounting for around 60% of an articulated hauler’s total mass and more than half of its emissions in the cradle-to-gate life cycle.
Cradle-to-gate is a model that assesses a product's environmental footprint from raw materials extraction until it leaves the factory-“gate”.
Growing sustainability plans
Volvo CE first introduced fossil-free steel in 2021 in partnership with Swedish steel producer SSAB, unveiling a concept hauler made from this material. In 2022, it became the first company to deliver a construction machine built with fossil-free steel to a customer.
Now, Volvo CE is scaling up its efforts by incorporating low-carbon emission steel—produced using recycled steel and powered by fossil-free electricity and biogas—into mass production.
Currently, 13% of the total steel mass in articulated haulers built at Braås has been replaced with this material, with plans to increase this proportion as supply chain availability grows.
This shift is expected to cut Volvo CE’s CO₂ emissions by approximately 13,000 tons per year, a reduction of over 5% within the cradle-to-gate scope.
Rickard Alm, head of Volvo CE’s Life Cycle Assessment (LCA) programme, said, “We are proud to lead the way in the industry and move forward towards minimising our climate footprint across the entire lifecycle of our products. While emissions from product use represent the vast majority of carbon output in our industry, it is important to also act to cut emissions in the production phase, including materials like steel, in close collaboration with our global supply partners.”
-
24 Feb 25 25 Feb 25
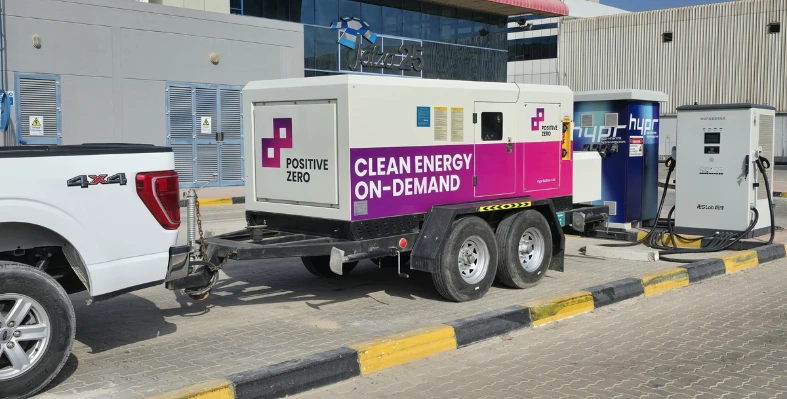
A major selling point of the HYPR Energy solution is its sustainability. (Image source: Positive Zero)
Bringing solar-powered mobile batteries to construction sites
In a conversation with Technical Review Middle East, Stanislav Betin, the general manager of HYPR Energy, a Positive Zero company, provided an in-depth overview of their innovative mobile battery system designed to power construction sites. A key focus was how these batteries are powered by renewable energy.
Betin explained the evolution of their electric power unit (EGPU), starting with a 175 kWh battery and upgrading to a 423 kWh battery mounted on a trailer. As he noted, "It's very mobile. We can bring it anywhere. We can mobilise the site within three to four hours." This mobility is a crucial advantage, allowing the system to be quickly deployed at construction sites.
A major selling point of the HYPR Energy solution is its sustainability. Betin emphasised that the system is "zero noise emitting, zero CO2 emitting" and often cheaper than traditional diesel generators. He explained how the company leverages its access to solar infrastructure, stating, "We also couple this product with our access to solar infrastructure across Dubai. We have 500+ different projects, and we are using the credits from those projects, which are accumulated over time. And we use those credits about the batteries. So we try to have this like a circular economy, omitting CO2 emission at every possible stage."
A data-driven approach
The real-time monitoring and fleet management capabilities of the system were also highlighted. As Betin noted, "Every element of our system, either the charger, battery, a port, even a truck, is IoT connected. So we see the real time location, and we also see all the key parameters for that specific element, like the state of charge and state of health." This data-driven approach allows the company to optimise operations and predict maintenance needs.
Betin acknowledged that the company faces some challenges in scaling up and quickly introducing their mobile battery system to the market. As he explained, "The challenge currently is the speed at which we should introduce the batteries to the market.”
Whenever peak power is required, the battery can sustain up to 250 kilowatt output
He noted that the temporary nature of construction sites requires frequent demobilisation and remobilisation of the battery systems, which adds complexity compared to more permanent solar installations. Betin said the company is working to address this by targeting clients with longer-term construction projects, up to 28 months, to provide more consistent service.
Despite these challenges, Betin expressed confidence in the company's ability to scale up, stating their plans to expand the battery fleet significantly this year, with new batches arriving in the coming weeks. He emphasised the strong demand they are seeing, driven by the booming construction sector and companies' focus on sustainability targets.
The role of digital twins in tackling water challenges
Gregg Herrin, Bentley Systems vice president for water, pens a piece on how digital twins can ensure sustainable practices and help conserve water. This is the first in a three-part series of his op-ed, which has been slightly edited for brevity. Read on.
When thinking about climate change, it is both accurate and enlightening to view the global environmental challenge as, primarily, a water crisis.
Climate change impacts water in several ways: regional droughts, dried-up lakes and riverbeds, torrential rain storms and floods, diminished water quality due to chemical or wastewater runoff, and overall concerns about water security.
These broad and multifaceted water problems are detrimental both to human health and our ecosystem.
As climate change continues to impact our natural resources and weather patterns, the need for sustainable and energy-efficient solutions for water management has never been direr.
Data-driven sustainability
Infrastructure digital twins offer some novel pathways for responding to the current global challenges related to water management.
Technologies such as smart meters, real-time data and predictive analytics, Internet of Things (IoT), AI, and digital twins can assist in water management projects through better monitoring and prediction, as well as improved decision-making capabilities, resulting in less water waste and protection against contamination of water supplies.
While other infrastructure areas, such as transportation and energy, have begun utilising digital twins more broadly, adoption has been somewhat slower in water management.
This slower adoption is often due to the complexity of water systems, the need for extensive data integration, and the traditionally conservative nature of the water management sector when it comes to adopting new technologies.
However, there are several key factors that are encouraging a more open stance toward the adoption of new technologies, including digital twins.
These include increasing regulatory and environmental pressures, ageing infrastructure with the need for modernisation, advancements in data collection and analytics, and increased focus on resilience and sustainability.
Proven success from early adopters of digital twin solutions is also helping drive confidence in the technology’s potential.
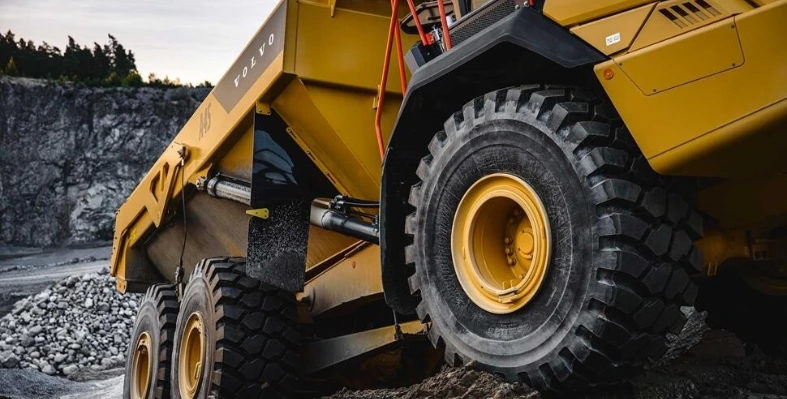
Steel is a major contributor to the carbon footprint of construction equipment. (Image source: Volvo CE)
Volvo CE's latest haulers now made with low-carbon steel
Volvo CE has begun integrating low-carbon emission steel into the serial production of all articulated haulers manufactured at its Braås facility in Sweden.
The company said that this move aligns with the company’s commitment to reducing carbon emissions across its value chain, both in machine operation and material sourcing, as part of its goal to reach net zero greenhouse gas emissions by 2040.
Steel is a major contributor to the carbon footprint of construction equipment, accounting for around 60% of an articulated hauler’s total mass and more than half of its emissions in the cradle-to-gate life cycle.
Cradle-to-gate is a model that assesses a product's environmental footprint from raw materials extraction until it leaves the factory-“gate”.
Growing sustainability plans
Volvo CE first introduced fossil-free steel in 2021 in partnership with Swedish steel producer SSAB, unveiling a concept hauler made from this material. In 2022, it became the first company to deliver a construction machine built with fossil-free steel to a customer.
Now, Volvo CE is scaling up its efforts by incorporating low-carbon emission steel—produced using recycled steel and powered by fossil-free electricity and biogas—into mass production.
Currently, 13% of the total steel mass in articulated haulers built at Braås has been replaced with this material, with plans to increase this proportion as supply chain availability grows.
This shift is expected to cut Volvo CE’s CO₂ emissions by approximately 13,000 tons per year, a reduction of over 5% within the cradle-to-gate scope.
Rickard Alm, head of Volvo CE’s Life Cycle Assessment (LCA) programme, said, “We are proud to lead the way in the industry and move forward towards minimising our climate footprint across the entire lifecycle of our products. While emissions from product use represent the vast majority of carbon output in our industry, it is important to also act to cut emissions in the production phase, including materials like steel, in close collaboration with our global supply partners.”
Egypt advances mining at Indaba 2025
Egypt’s Minister of Petroleum and Mineral Resources, Karim Badawi, spoke at the ministerial session of African Mining Indaba, held in Cape Town from 3–6 February 2025
The session, themed “Forging a United African Mining Front: Collaboration for Sustainable Development,” brought together key leaders, including South Africa’s Minister of Mineral Resources and Petroleum, Gwede Mantashe; the Democratic Republic of Congo’s Minister of Mines, Kizito Pakabomba Kapinga Mulume; and Zambia’s Minister of Mines and Mineral Development, Paul Kabuswe. The discussion was moderated by Marit Kitao, Director of the African Mineral Development Centre.
Badawi outlined Egypt’s progress in modernising its mining sector, emphasising that reforms are beginning to yield tangible results. He highlighted the country’s vast mineral potential and the government’s commitment to attracting investment through its new programme, which aligns with Egypt Vision 2030. The goal is to position Egypt as a key player in the global mining industry.
Modernisation
He also underscored Egypt’s dedication to fostering sustainable partnerships in the mining sector. He pointed to the recent finalisation of an updated Mineral Exploitation Agreement Model as evidence of efforts to enhance the investment climate. This new framework, he noted, is designed to create mutual benefits for stakeholders while supporting comprehensive modernisation strategies.
Further, Badawi detailed ongoing efforts to develop strategies for value-added mining industries and for managing the environmental and social impacts of mining activities. He also outlined the country’s strategy for maximising critical minerals to support the energy transition.
He announced plans for the Egyptian Digital Mining Platform, modeled after the Egyptian Upstream Gateway (EUG), which will offer detailed geological data and facilitate transparent investor engagement with the Egyptian Mineral Resources Authority.
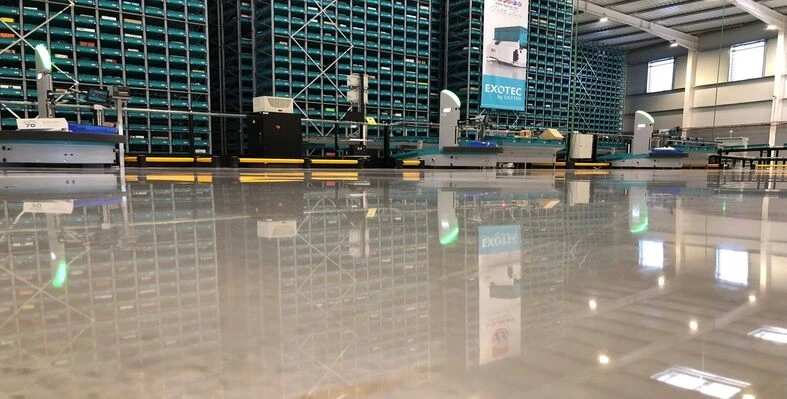
The company's global presence includes manufacturing facilities in Belgium. (Image source: Convergent)
Convergent Group's winning solutions
We're not just a group that created the best lithium silicate hardeners in 2000, we're first and foremost a research team for the protection of concrete surfaces in general.
It’s the most preferred and specified brand by design builders, architects and owners and it continues to set the standard by which all others follow.
Over the past 25 years, we have continued to develop our lithium-based products to bring you a complete range from hardeners to solid & transparent colours, to finishing products as well as lithium-based detergents.
Finishing a concrete surface is a piece of patience and knowledge!
That’s why we have around the world 50 distributors, who are expert in concrete surfaces with more than 100 million sqm experience.
With our research department, we have developed other hardeners, other pigments, other finishing products, other waterproofing products based on different silicates such as sodium, potassium, fluorine, but also hardeners based on colloidal silica, repair mortars that you can colour, but also a range polyaspartic products.
Facility owners from various industries have relied on our unique chemical strengths to make their concrete and masonry cleaner, safer and more durable:
Aeronautic: Boeing, Airbus
Concrete Highway, Landing Strip, Haven)
Manufacturing: Inditex, Louis Vuitton
Car & Truck factories: Scania, Iveco, VAG, Mercedes
Nuclear Site: Spain
Shopping mole: Lotus Shopping
Grocery stores: Aldi, Metro, Gran Mercado, Carrefour, Atacadao
Water & Soda Production: Coke, Utah Juice
Warehousing: Amazon- E-Mag, Nestlé
Commercial: Ikea, Leroy Merlin, Castorama
Healthcare & Hospital, Universities: Brussel’s, Helsinki
Cold rooms & Freezers: Mc Cain
Perfumes production: Dior
Luxury Stores: Hermes
Pharmaceutical: Pfizer
Museum: Guggenheim
This article was written by Convergent Group SA, which is an international chemicals company based in Belgium, specialising in the manufacture of chemical treatments for concrete surfaces.
The company's global presence includes manufacturing facilities in Belgium and distribution networks serving Europe, Africa, Australia/New Zealand, India, and the Middle East.
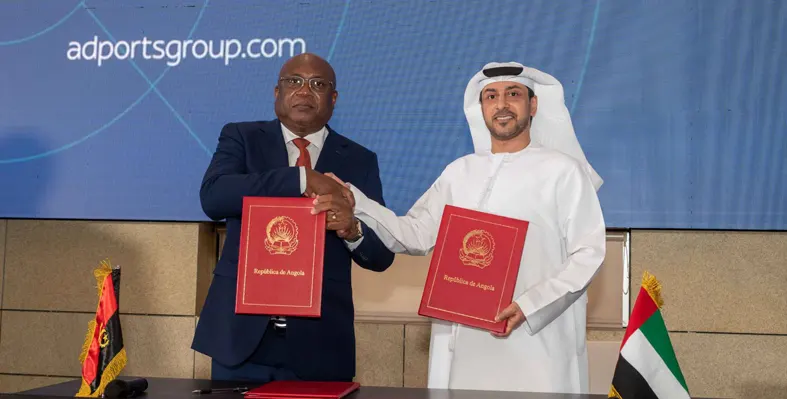
AD Ports Group begins managing Luanda’s multipurpose terminal and logistics venture. (Image source: AD Ports)
AD Ports invests in Angolan logistics
AD Ports Group, a prominent player in global trade, logistics, and industry has began overseeing the long-term management and development of a major multipurpose terminal and an accompanying logistics venture in collaboration with local partners in Luanda, Angola, marking a significant step in the company’s expansion across sub-Saharan Africa
Partnering with Unicargas and Multiparques, AD Ports Group has commenced operations at the Noatum Ports Luanda Terminal, situated at Angola’s largest port. The Port of Luanda accounts for approximately 76% of the country’s container and general cargo traffic and offers vital maritime connections to neighbouring landlocked nations like the Democratic Republic of the Congo and Zambia.
AD Ports Group holds an 81% stake in the multipurpose terminal joint venture, while it owns 90% of the logistics venture with Unicargas.
The agreement, a 20-year concession with the Luanda Port Authority signed in April 2024, includes an investment commitment of around US$250mn by AD Ports Group through 2026 for the modernization of the terminal and the establishment of Noatum Unicargas Logistics. This joint venture will provide comprehensive logistics, transport, and freight forwarding services to regional, local, and international clients.
With the terminal now operational, Noatum Unicargas Logistics has also begun trading. The logistics business is making substantial investments in new trucks and systems and will be fully integrated into the Noatum Logistics global network, improving Angola’s connectivity to international markets and driving growth in the national economy.
Based on market demand, AD Ports Group’s total investment in this project could increase to USD 380 million over the duration of the concession, which may be extended by an additional decade.
In late 2024, AD Ports Group also secured two agreements with the Angolan government that provide substantial tax and financial advantages to its operating subsidiaries.
These investments are expected to create thousands of direct and indirect jobs, alongside a focus on training and skill development. The planned upgrades will also introduce environmentally sustainable technologies, ensuring lower carbon emissions.
Mohamed Eidha Al Menhali, regional CEO of AD Ports Group, commented, “With the planned upgrade of Luanda’s multipurpose port terminal, and the establishment of an integrated logistics and freight forwarding business leveraging our Group’s global network and reach, AD Ports Group is positioned to capture the growth in Angola’s container volumes, which are forecast to rise on average by 3.3% annually over the next decade. In line with the direction of our wise leadership, this significant investment by our Group and its partners will strengthen the country’s ties with the UAE and bring jobs and economic prosperity to the citizens of Angola.”
Ricardo Daniel Sandão Queirós Viegas de Abreu, minister of transport, Angola, stated, “The Port of Luanda is the main maritime gateway to Angola, a critical hub for regional trade and an economic lifeline for the region. Our strategic partnership with AD Ports Group, part of a broader effort involving multiple stakeholders, will transform the Port of Luanda into an efficient, high-performance multipurpose facility that transforms our logistical capabilities and drives economic growth across central West Africa. This collaboration is a significant milestone in our mission to modernise infrastructure and expand access to global trade, while delivering a prosperous future to Angola and its partners."